Selecting the best options for warehouse storage involves careful consideration of various factors, including the type of goods being stored, available space, accessibility requirements, and budget constraints. As an expert in warehouse management, we recommend evaluating the following options to optimise storage efficiency and maximise space utilisation:
Selective Pallet Racking
Selective pallet racking is one of the most common and versatile storage systems used in warehouses. It consists of upright frames and horizontal load beams that can be adjusted to accommodate different pallet sizes and configurations. This system provides direct access to each pallet, making it ideal for warehouses with a high variety of SKUs and frequent inventory turnover.
Drive-In and Drive-Through Racking
Drive-in and drive-through racking systems are designed for high-density storage of homogeneous products with low turnover rates. In drive-in racking, pallets are loaded and retrieved from the same aisle, while drive-through racking allows access from both sides of the system. These systems maximise storage space by eliminating aisles between racks, but they sacrifice some selectivity and accessibility.
Push Back Racking
Push back racking systems utilise inclined rails and nested carts to store pallets in a Last-In, First-Out (LIFO) configuration. This system allows for dense storage of multiple SKUs while maintaining relatively high selectivity compared to drive-in racking. Push back racking is suitable for warehouses with moderate inventory turnover and a mix of SKUs.
Cantilever Racking
Cantilever racking is designed for storing long, bulky, or irregularly shaped items such as lumber, piping, or furniture. It features horizontal arms that extend from upright columns, providing easy access to stored items without obstruction from vertical supports. Cantilever racking is adjustable to accommodate varying item sizes and lengths.
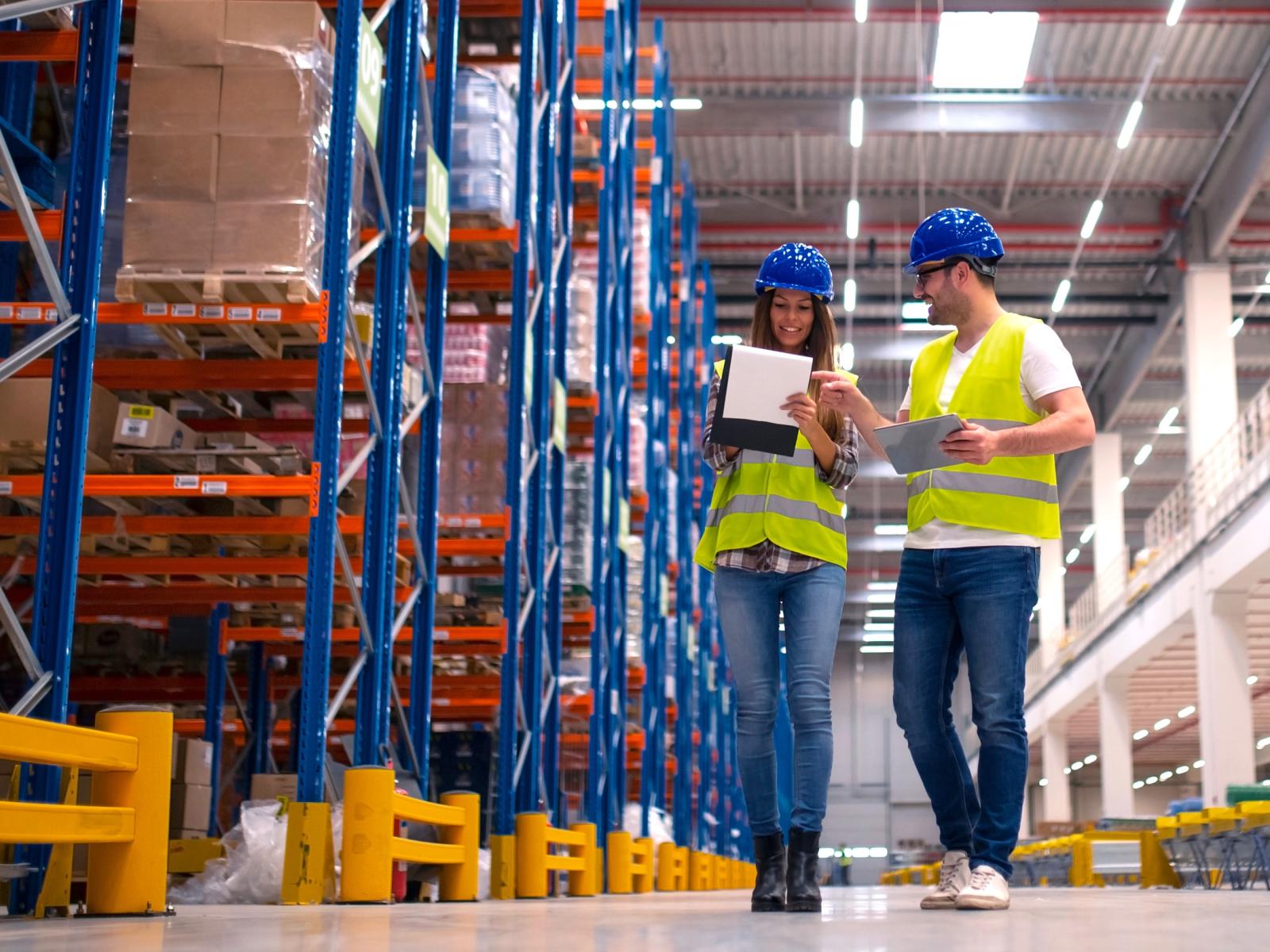
Carton Flow Racking
Carton flow racking, also known as gravity flow racking, is a dynamic storage system that utilises inclined roller tracks or conveyor lanes to facilitate FIFO (First-In, First-Out) picking of cartons or boxes. This system is ideal for warehouses with high-volume order picking operations and fast-moving inventory, as it promotes efficient stock rotation and order fulfilment.
Mezzanine Floors
Mezzanine floors are intermediate levels constructed within the warehouse space to create additional storage or workspace. Mezzanines can be used to increase storage capacity without expanding the footprint of the warehouse, making them cost-effective solutions for maximising vertical space. They are suitable for storing lightweight or bulky items that do not require palletised storage.
Vertical Lift Modules (VLMs)
Vertical lift modules are automated storage systems that utilise vertical carousels to retrieve and store items stored in trays or bins. VLMs maximise storage density by utilising the full height of the warehouse, while also providing high-speed retrieval and accurate inventory management. VLMs are suitable for warehouses with limited floor space and high-value or small parts inventory.